Introduction
In today's fast-paced world, reliable power generation is essential for various industries, businesses, and households. Diesel generators have long been a popular choice for providing backup power in case of grid failures or as a primary source of electricity in remote locations. However, the efficiency of diesel generators can vary depending on several factors, including maintenance practices, load management, and fuel quality. In this article, we will explore how to optimize the efficiency of diesel generators to ensure peak performance and reduce operational costs.
Understanding Diesel Generators
Diesel generators are widely used in a variety of applications due to their reliability, durability, and ability to provide high power output. These generators operate by converting the chemical energy of diesel fuel into mechanical energy through a combustion process. The mechanical energy is then converted into electrical energy using an alternator, which produces the desired voltage and frequency for the connected load.
Diesel generators are available in various sizes and configurations to meet the specific power requirements of different applications. They can be used for standby power, prime power, or continuous power applications, depending on the intended use and operating conditions. Standby generators are typically used as backup power sources and are activated during grid outages or emergencies. Prime power generators are designed for continuous operation and can be used as the primary source of electricity in remote locations or off-grid sites. Continuous power generators are designed for long-term operation and can provide power for extended periods without interruption.
Factors Affecting Diesel Generator Efficiency
Several factors can impact the efficiency of diesel generators, affecting their overall performance and operational costs. It is essential to consider these factors when optimizing the efficiency of a diesel generator:
1. Maintenance Practices: Regular maintenance is crucial for ensuring the efficient operation of diesel generators. Proper maintenance includes routine inspection, cleaning, lubrication, and servicing of critical components such as the engine, alternator, fuel system, and cooling system. Neglecting maintenance can lead to increased fuel consumption, reduced power output, and higher maintenance costs over time.
2. Load Management: Efficient load management is essential for optimizing the performance of diesel generators. Operating a generator at partial load or overload conditions can reduce its efficiency and increase fuel consumption. It is important to match the generator's output with the connected load to ensure optimal fuel efficiency and performance.
3. Fuel Quality: The quality of diesel fuel used in a generator can significantly impact its efficiency and performance. Low-quality fuel with high levels of contaminants or impurities can lead to engine deposits, reduced combustion efficiency, and increased emissions. Using high-quality, clean diesel fuel with the right specifications is essential for maximizing the efficiency of a diesel generator.
4. Operating Conditions: The operating conditions of a diesel generator, such as ambient temperature, humidity, altitude, and load profile, can affect its efficiency and performance. Extreme environmental conditions can impact the cooling system, combustion process, and overall engine performance. It is important to consider these factors when optimizing the efficiency of a diesel generator for specific applications.
Efficiency Optimization Techniques
To maximize the efficiency of a diesel generator and ensure peak performance, several optimization techniques can be employed. These techniques focus on improving maintenance practices, load management strategies, fuel quality, and operating conditions to enhance the overall efficiency of the generator. Some of the key efficiency optimization techniques for diesel generators include:
1. Regular Maintenance: Implementing a comprehensive maintenance schedule is essential for ensuring the efficient operation of a diesel generator. Regular maintenance tasks include checking fluid levels, inspecting components for wear and tear, cleaning filters, and testing critical systems such as the fuel system, cooling system, and electrical system. By following a structured maintenance plan, operators can prevent costly breakdowns, optimize performance, and extend the lifespan of the generator.
2. Load Testing and Monitoring: Conducting regular load tests and monitoring the generator's performance under varying load conditions can help optimize fuel efficiency and performance. By simulating different load profiles and adjusting the generator's output accordingly, operators can identify the optimal operating range for maximum efficiency. Load testing also helps detect any issues with the generator's capacity, voltage regulation, and fuel consumption, allowing for timely adjustments and optimizations.
3. Fuel Management: Proper fuel management is essential for maximizing the efficiency of a diesel generator. This includes using high-quality fuel with the right specifications, storing fuel properly to prevent contamination, and monitoring fuel consumption to detect any anomalies. By maintaining a clean fuel supply and ensuring proper fuel delivery to the engine, operators can improve combustion efficiency, reduce emissions, and optimize fuel consumption.
4. Cooling System Optimization: The cooling system plays a crucial role in maintaining the optimal operating temperature of the diesel generator. Regular inspection of the cooling system components, such as the radiator, coolant, hoses, and fans, is essential for preventing overheating and ensuring efficient engine performance. By keeping the cooling system well-maintained and operating within the recommended temperature range, operators can enhance the efficiency and reliability of the generator.
5. Emission Control: Diesel generators are known for their high emissions of pollutants such as nitrogen oxides (NOx), particulate matter (PM), and carbon monoxide (CO). Implementing emission control measures, such as installing exhaust gas after-treatment systems, using cleaner fuel, and optimizing combustion processes, can help reduce emissions and improve the environmental performance of the generator. By complying with regulatory standards and implementing emission reduction technologies, operators can enhance the efficiency and sustainability of their diesel generators.
6. Remote Monitoring and Control: Utilizing remote monitoring and control systems can help optimize the efficiency of diesel generators by providing real-time data on performance metrics, fuel consumption, load profiles, and operating conditions. Remote monitoring systems enable operators to track the generator's performance from a centralized location, identify potential issues proactively, and make timely adjustments to optimize efficiency. By leveraging advanced monitoring technologies, operators can improve the reliability, availability, and efficiency of their diesel generators.
Case Studies and Best Practices
To illustrate the practical application of efficiency optimization techniques for diesel generators, let's consider a few case studies and best practices adopted by industry leaders:
Case Study 1: Industrial Manufacturing Plant
An industrial manufacturing plant relies on diesel generators for backup power during grid outages and peak demand periods. To optimize the efficiency of their generators, the plant implemented a comprehensive maintenance program that includes regular inspection, servicing, and testing of critical components. They also conducted load testing to determine the optimal operating range for maximum efficiency and adjusted the load profile accordingly. By monitoring fuel consumption and implementing emission control measures, the plant was able to reduce operational costs, improve reliability, and enhance the overall performance of their diesel generators.
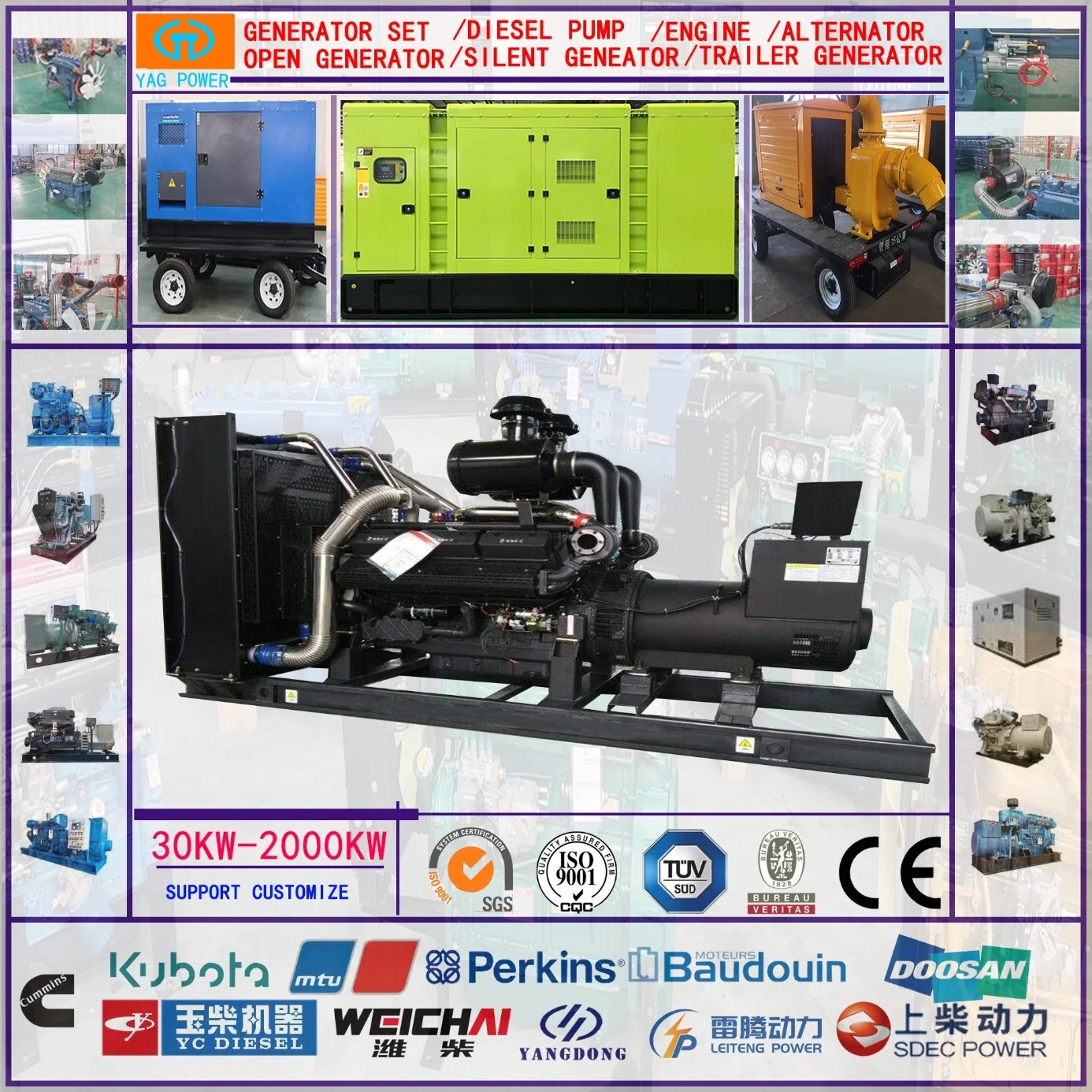
Best Practice 1: Implementing a Preventive Maintenance Plan
Developing a preventive maintenance plan is essential for maximizing the efficiency and longevity of diesel generators. 300kw diesel generator for remote offices should include routine inspection, cleaning, lubrication, and testing of key components to prevent breakdowns and optimize performance. By following a structured maintenance schedule and addressing issues proactively, operators can minimize downtime, reduce maintenance costs, and ensure the reliable operation of their generators.
Case Study 2: Data Center Facility
A data center facility relies on diesel generators for backup power in case of grid failures or emergencies. To optimize the efficiency of their generators, the facility implemented a fuel management strategy that includes using high-quality fuel with the right specifications, monitoring fuel consumption, and maintaining a clean fuel supply. They also optimized the cooling system to prevent overheating and ensure efficient engine performance. By leveraging remote monitoring and control systems, the facility was able to track the performance of their generators in real-time, identify potential issues, and make proactive adjustments to enhance efficiency and reliability.
Best Practice 2: Conducting Regular Load Testing
Conducting regular load tests is essential for optimizing the performance and efficiency of diesel generators. By simulating different load profiles and adjusting the generator's output accordingly, operators can identify the optimal operating range for maximum efficiency. Load testing also helps detect any issues with the generator's capacity, voltage regulation, and fuel consumption, allowing for timely adjustments and optimizations to improve overall performance.
Conclusion
Optimizing the efficiency of diesel generators is essential for ensuring reliable power generation, reducing operational costs, and enhancing sustainability. By implementing maintenance best practices, load management strategies, fuel quality measures, and emission control technologies, operators can maximize the performance and efficiency of their generators. It is crucial to consider factors such as maintenance practices, load management, fuel quality, and operating conditions when optimizing the efficiency of diesel generators for specific applications. By following best practices, conducting regular maintenance, monitoring performance metrics, and leveraging advanced technologies, operators can achieve peak efficiency and performance from their diesel generators.